Seventeen (17) employees undergoing the second part of their advanced training for boiler at the Ramu NiCo’s Basamuk (BSK) Refinery for more than two weeks in January 2024 and are proud to receive their certificates.
Yearly training on health and safety has been the tradition of the RNML ever since the company started and went into full production.
Now, however, training does not merely focus on upholding the safety alone but importantly looks onto improving the skills and knowledge on the operations of the equipment used both at the mine and refinery.
Michael James Tait, the training manager for the Ramu Nickel and Cobalt project in Madang engaged on theory and practical training on the operation of equipment at the refinery.
One of the theory and practical training covered was on the operation of the boilers. The boiler plant producing large mass of steam that hits up the Slurry Nickel and Cobalt ores piped from the mine at Kurumbukari to the Refinery at Basamuk.
It is then condensed using high pressure acid leaching technology to produce Nickel metal and Cobalt salt.
The training is expected to complete assessment next month. He said certificates would be given to those who passed the assessment and would become trainers in the future.
There are total of seventeen employees going through the training with thirteen are locals and four are Chinese.
Having good level of knowledge on the use of the equipment is better for employees at the mine site and the refinery.
Mr. Tait said overall training would cover more 1200 employees both nationals and expatriates from 2016 up to now including Health Safety and Environment, Process training for upskilling of process plant operators, and Trades training.
Boiler Operator, Tonny Apkimb a trainee who had served the company for thirteen (13) years shared his experience. He thanked the RNML for making this training possible for him and his co-workers.
“There is no such boiler training in the country, and I am fortunate and thankful for the company for providing such training in the workplace that enhanced my knowledge and skill,” Apkimb said.
Based on the Memorandum of Agreement (MoA), RNML is committed and striving to provide training and localization plan to provide more job opportunities to local people, increase their family income and achieve long-term skill transfer through systematic training since the project commenced.
RNML have in place a set of comprehensive training policies and systems for its employees. The training focuses on the need of company’s operation and talent development. It aims to assist employees to quickly adapt to the posts, enhance their competency and support to build up the international competitiveness of the company.
The competency-based training and assessments are delivered from in-house training modules developed by trainers to Australian Qualification Framework (AQF), New Zealand Qualification Framework (NQF) and the National Apprenticeship and Trade Testing Board (NATTB) Standards at the Basamuk Refinery facilitated by Ramu NiCo Management (MCC) Limited (RNML).
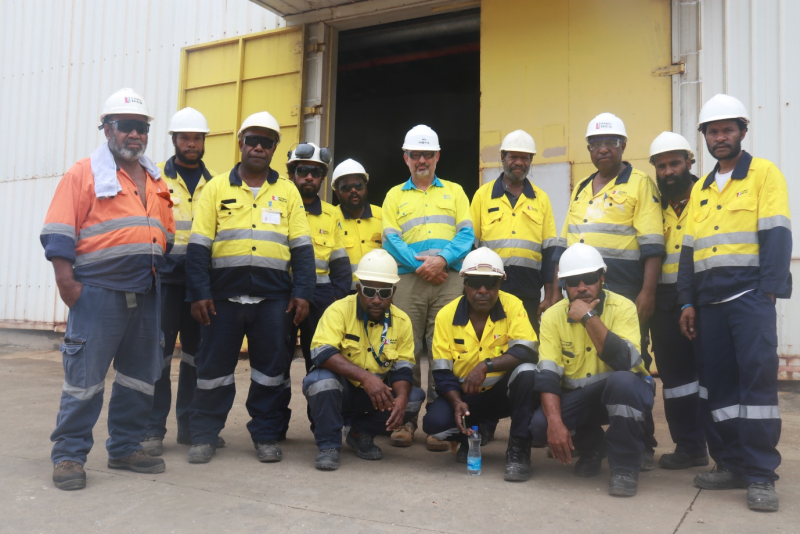
BKS Refinery boiler trainees and their trainer pause for a photo before the technical site visit
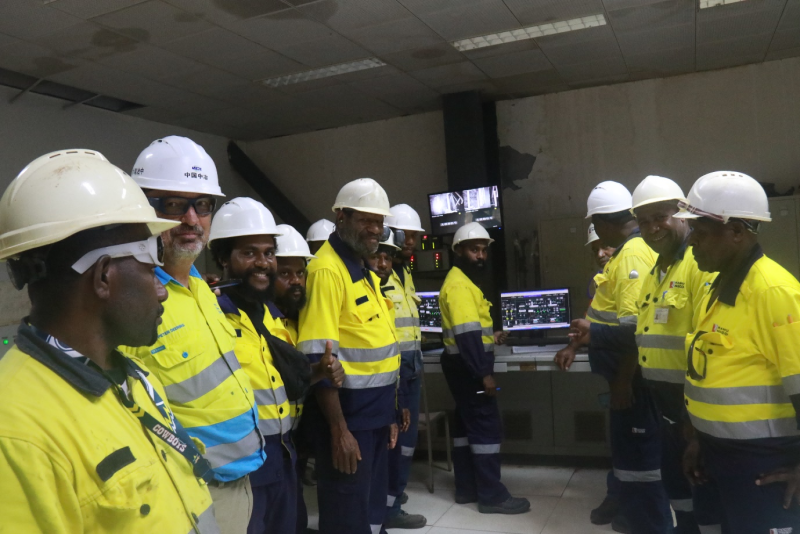
Inside the boiler monitoring section
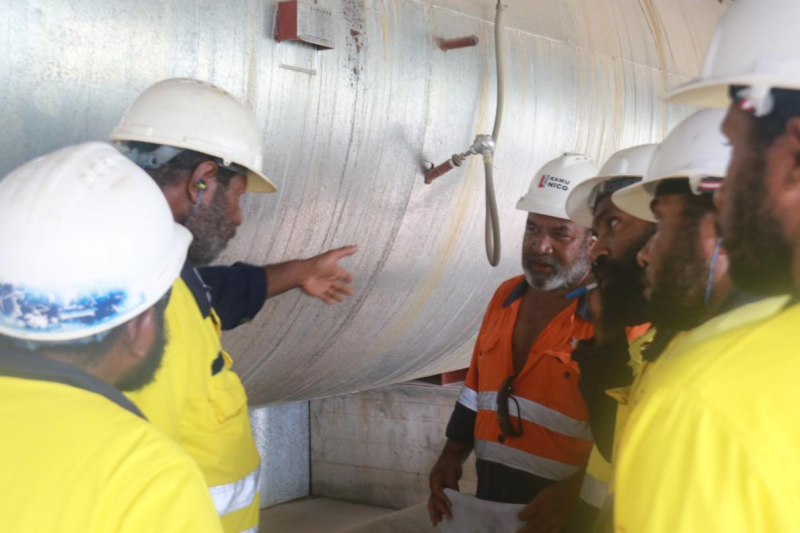
Standing next to the boiler
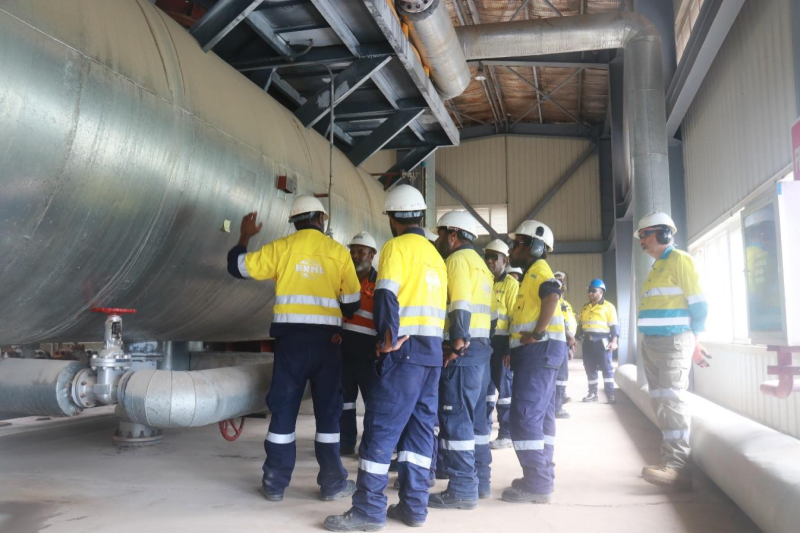
Standing next to the boiler
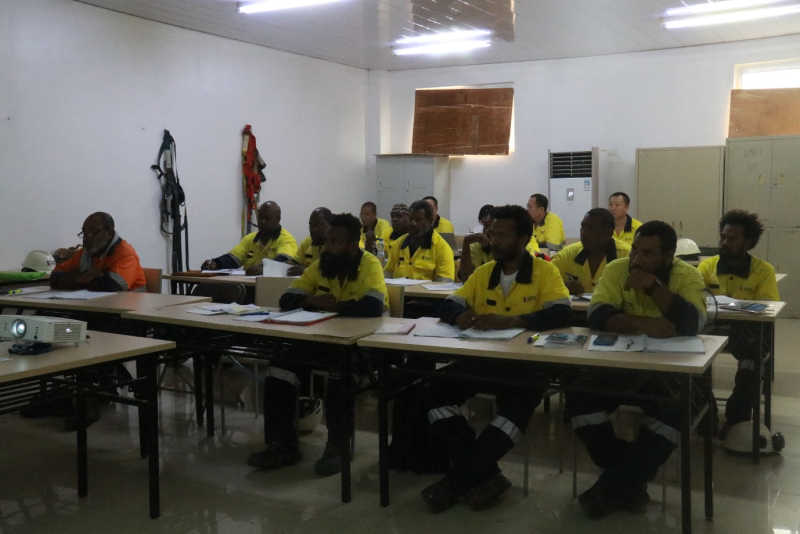
During class time