中冶瑞木冶炼厂精益管理各专项小组火力全开,克服重重困难,攻克道道难关,以坚实有序的步伐在精益管理的新征程阔步前行,首月工作成果斐然,为后续的深度推进带来希望。
6S与可视化组精心打造了中和产品作业区E149一楼产品包装区这一“样板间”,并迅速在128区域“复制粘贴”成功经验,主控室也旧貌换新颜。移动作业区停车区域的6S改造正如火如荼,同时明确了工作区域的必要物与不必要物标准,为规范作业区管理立下“规矩”。后续,他们将朝着全面覆盖各作业区的目标,持续深化6S改造,并建立起长效维护机制。尽管面临着人员捉襟见肘的困难,16个作业区的工作人员需在本职与6S工作间“辗转腾挪”,但各作业区对精益理念的高度认同和积极响应,成为了6S工作顺利推进的有力保障,让这片“试验田”得以茁壮成长。
日常管理组的工作同样可圈可点。他们精心制定的各作业区指标明细表,借助三色图清晰呈现,让人一目了然。看板模板敲定后,涵盖作业区组织架构、改善动态、计划与案例等丰富内容,已在各作业区“安家落户”,并强化了日常巡检工作,为生产运营筑牢安全与合规的“堤坝”。接下来,他们将聚焦于看板的全面落地与数据指标的深度剖析,挖掘实际与目标间的差距根源。指标制定过程宛如在“走钢丝”,既要贴合工艺设计的科学性,又要预留生产提升的空间,其抽象性也增加了理解与执行的难度,加之看板定制的延迟,一度使工作陷入僵局。但在指导老师的帮助和指导下,他们成功另辟蹊径,通过模拟看板推动工作继续“航行”。
标准作业组在SOP编制的海洋中奋力遨游,梳理出513份明细,精准锚定工艺技术操作规程的编制重点,将任务逐月分解。成员们依循SOP关键要素精心雕琢,已成功完成7份SOP样本及部分工艺技术操作规程编制,成果初绽。后续,他们将按部就班推进多项工艺技术操作规程的修订与初稿编制,并依据标准模板拓展其他标准作业规程文件的编制版图。工艺技术操作规程编制犹如攀登高峰,专业性强、难度大,但小组成员们群策群力,搭建起科学的编制框架,成功迈出坚实步伐。
TPM组对第二台样板设备换胎机进行了全方位“体检”与修复,从滑道清理到外壳修复,从线路整合到部件漏油处理,事无巨细,并完善了点检文件体系,向员工悉心传授点检要点。下一站,他们将以换胎机为蓝本对锁管机进行整改升级。然而,设备的“老龄”问题带来线路老化、部件磨损等隐患,整改时间长、人手短缺也成为“绊脚石”。但他们未雨绸缪,每次整改前仔细排查风险,作业区也全力协调人手,保障了精益改造与日常工作的“双轨并行”。
五星班组紧密结合冶炼厂实际,组建了10个小组,精心规划班组长职责与五星班组评价标准初稿,通过精益培训为班组成员“充电赋能”。HPAL生产A班与ERT应急班已在精益改善的道路上收获颇丰,看板设计也圆满完成。未来,他们将朝着打造一星班组的目标进发,逐步完善精益管理体系。工作起步时的迷茫,在指导老师的引领与团队的自我探索下,已化作照亮前路的光芒。
首月的精益管理之路,虽荆棘丛生,但冶炼厂各小组凭借坚韧不拔的毅力和创新求变的智慧,在挑战中淬炼,于困境中突破,取得了令人瞩目的阶段性成果。随着精益管理的持续深耕,冶炼厂必将在提升生产效率、优化作业环境、强化团队协作等方面不断提升,有力助推公司的高质量发展。
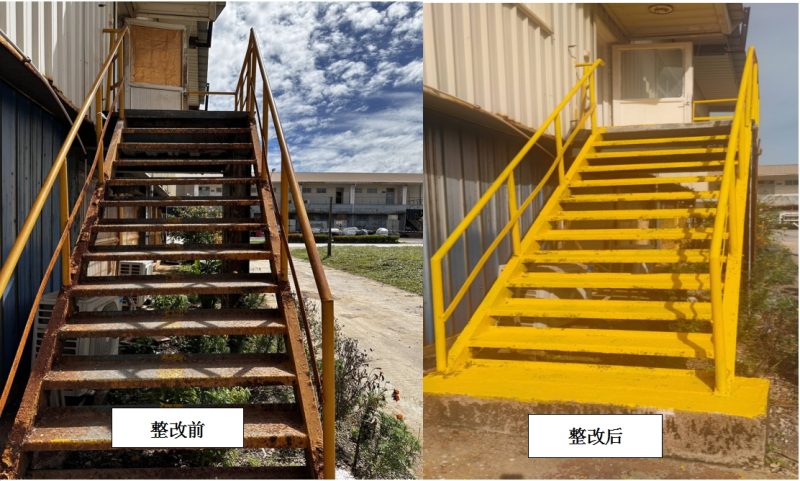
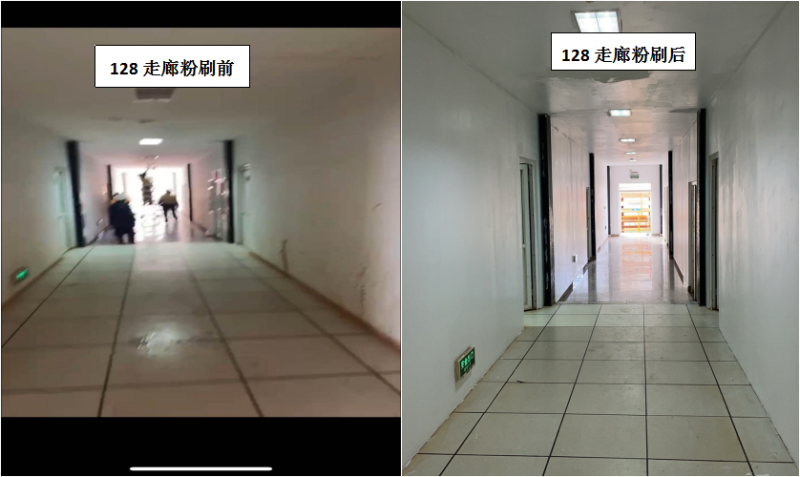
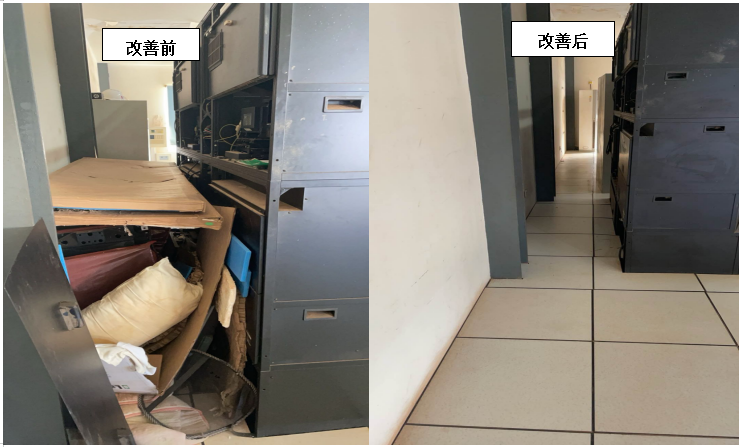
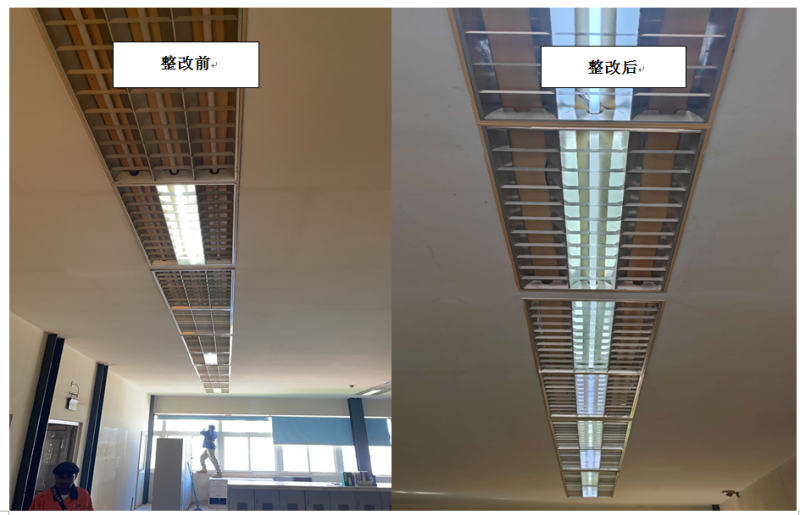
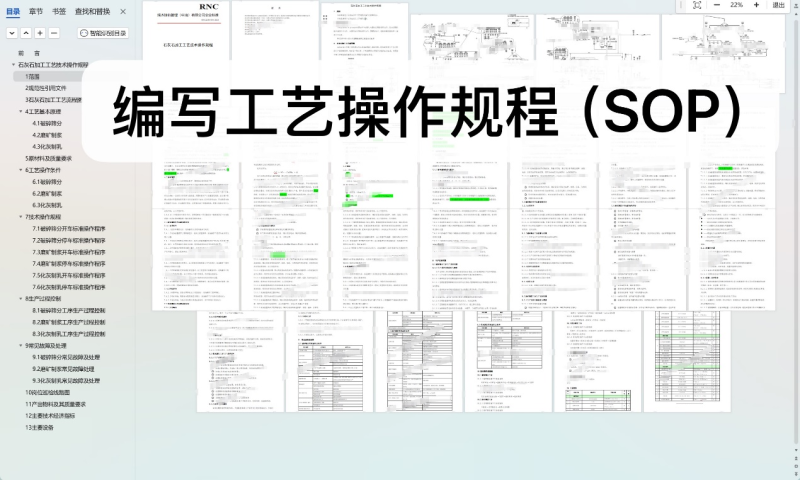